Manufacturers around the world are increasingly turning to aluminum extrusions as a cost-effective and efficient solution for their production needs. Aluminum extrusions offer many advantages, from providing strong support to creating complex shapes with ease.
This guide will provide an overview of why manufacturers are embracing aluminum extrusions and how they can be used to unlock new levels of efficiency in production processes. We’ll explore the benefits that aluminum extrusion provides, including its strength, light weight, durability, and versatility. Well also discuss how manufacturers can use aluminum extrusion technology to produce products quickly and efficiently while staying within budget constraints.
Finally, we’ll look at some tips on selecting the right type of extrusion for your specific application so you can get maximum return on your investment in this powerful technology.
Introduction to Aluminum Extrusions and their Benefits

Aluminum extrusions have been used in manufacturing for decades, and it’s no wonder why: they provide several unique benefits that make them an attractive choice. From their lightweight structure to their strong yet malleable nature, aluminum extrusions offer manufacturers the perfect combination of flexibility and reliability.
In this guide, we will explore what makes aluminum extrusions so advantageous and how they can be used to unlock greater efficiency in production processes. Aluminum is incredibly versatile – it’s light enough to transport with ease but strong enough for even the most demanding applications.
Extrusion combines these properties with a shape-shifting ability that allows manufacturers to create complex components from simple forms. Aluminum’s resistance to corrosion also means it can withstand tougher conditions than other metals or alloys, making it ideal for outdoor use as well as indoor applications where humidity or moisture may be present. Using advanced extrusion techniques available today, manufacturers now have access to greater precision when creating custom parts, allowing them to save time and money while still achieving desired results.
This process also opens up possibilities such as producing multiple pieces at once instead of one piece at a time which further reduces costs associated with materials handling and setup times on machines like CNC lathes or milling centers. The end result is improved productivity across the board – something any manufacturer can appreciate!
Maximizing Efficiency with Aluminum Extrusions
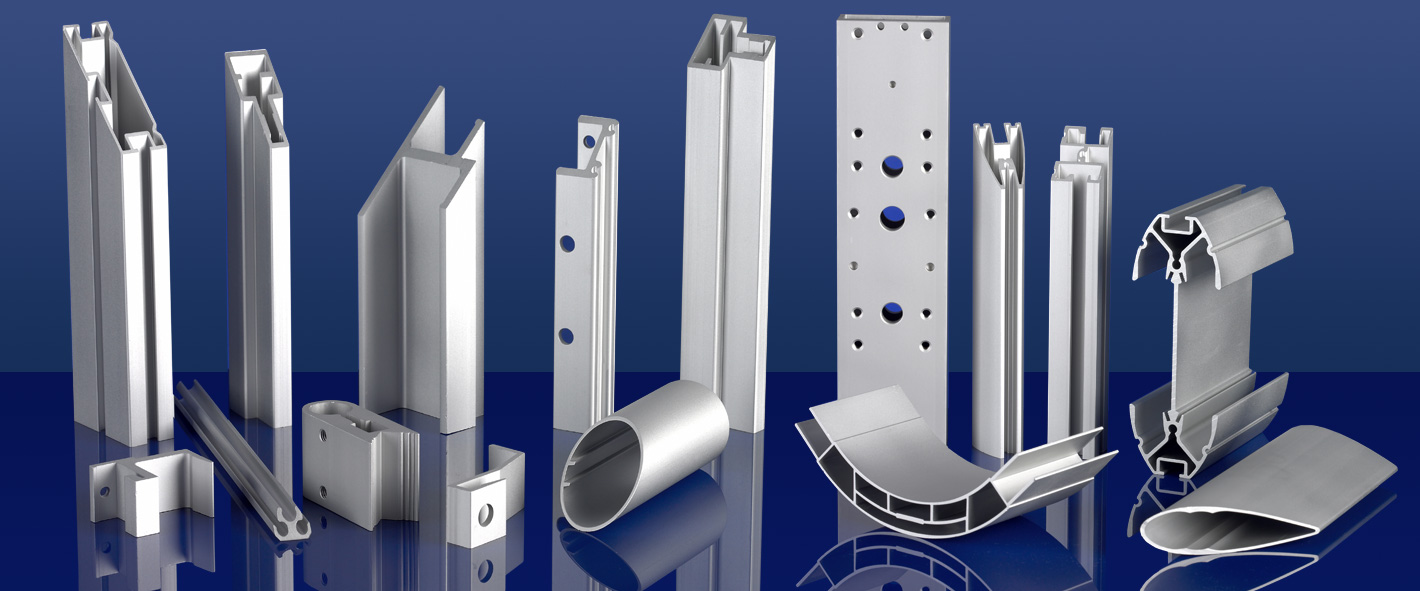
Aluminum extrusions are the key to unlocking efficiency for manufacturers and other businesses. As one of the most malleable metals available, aluminum extrusion offers a variety of benefits that can optimize productivity and minimize costs. Not only is aluminum corrosion-resistant, but it’s also light, strong, non-toxic, and can be easily machined into custom shapes or sizes based on an individual’s needs.
The process of creating extruded products is both fast and efficient since it requires no welding or heat treatment. This allows manufacturers to form objects quickly while maintaining tight tolerances in design specifications.
Furthermore, these methods make it much easier to keep production consistent due to the uniformity provided by repeated operations such as cutting or punching along each length of material used in fabrication. When considering how best to maximize efficiency with aluminum extrusions several factors should be taken into account.
For instance, complex pieces may require multiple steps during production which can lead to increased costs if not properly managed from start to finish. Likewise, certain types of materials may have limited availability leading to some projects needing more extensive planning than others before getting started on manufacturing processes themselves.
Working closely with a supplier who understands all the nuances associated with different extrusions will help ensure success when working on any project involving this type of metalwork product development. In conclusion, having a clear understanding of how best to utilize aluminum extrusions helps unlock potential savings throughout any manufacturing process while ensuring quality results time after time!
Design Considerations for Manufacturers Utilizing Aluminum Extrusions
Design considerations for manufacturers utilizing aluminum extrusions are immense. From customizing the extrusion profile to selecting from a variety of alloys, there is no shortage of decisions to be made to maximize efficiency and quality.
The strength-to-weight ratio that aluminum offers means that parts can now be designed more efficiently and with greater functionality than ever before. A manufacturer should consider the entire design process when working with aluminum extrusions, including how much material is needed, which alloy will provide optimal performance, and whether or not any special finishing options must be applied.
Furthermore, taking into account factors such as tolerances and surface finishes can help ensure that parts meet exact specifications. Ultimately, careful consideration throughout the design process will lead to increased productivity and cost savings down the line while unlocking efficiency with aluminum extrusions.
Conclusion
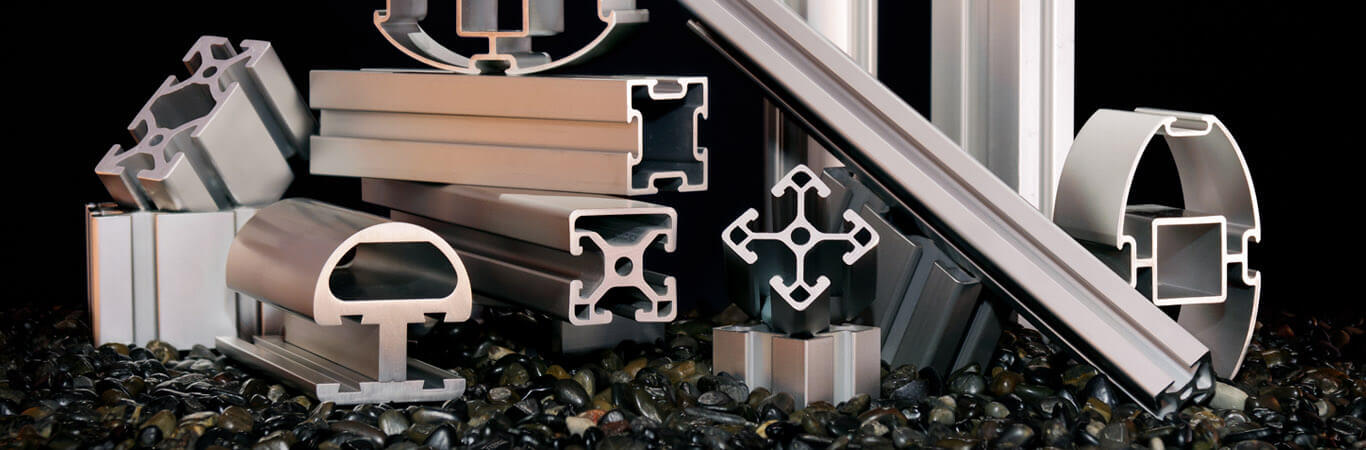
Aluminum extrusions are a great tool for manufacturers to increase efficiency, reduce costs, and improve product quality. 7075 aluminum extrusion is especially beneficial due to its exceptional strength-to-weight ratio, corrosion resistance, machinability, and ability to be welded or bonded with other metals. With the right techniques and tools, manufacturers can maximize the benefits of aluminum extrusions while reducing lead times.
Understanding their capabilities and limitations will help ensure that they are used efficiently and yield maximum results.